Metallurgy Interview Questions And Answers
Optimize your Metallurgy interview preparation with our curated set of 70 questions. These questions are specifically selected to challenge and enhance your knowledge in Metallurgy. Perfect for all proficiency levels, they are key to your interview success. Download the free PDF now to get all 70 questions and ensure you're well-prepared for your Metallurgy interview. This resource is perfect for in-depth preparation and boosting your confidence.
70 Metallurgy Questions and Answers:
Metallurgy Job Interview Questions Table of Contents:
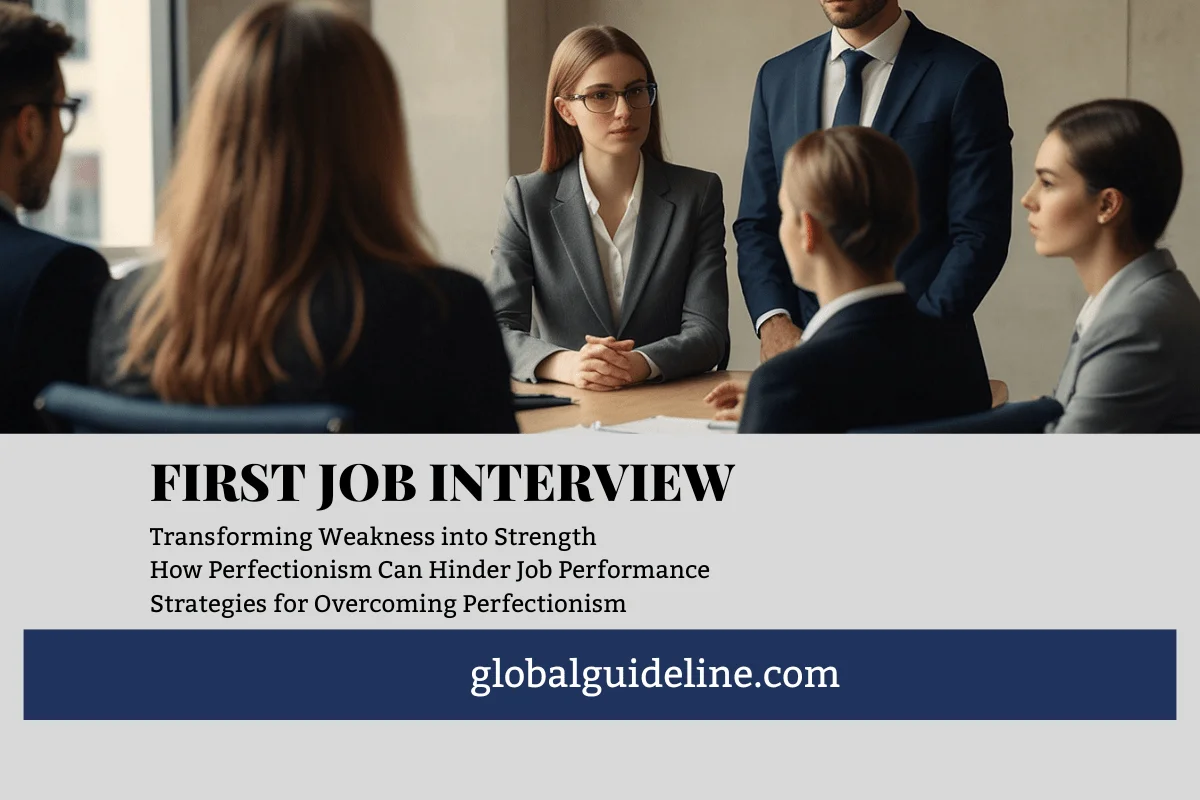
1 :: What is carbide?
The epsilon carbide is transition carbide of between Fe2C and Fe3C composition, with hexagonal close packing microstructure, which forms over a range of 250-400 ºC temperature during lower-bainite transformation. This transformation happens during tempering heat treatment of quenched steels, or during slow cooling in that temperature range.
It is fine dispersed carbide in a ferrite needle-like matrix. Lower bainite has lower tensile strength (about 5-10%), but usually same hardness as martensite structures, but with a higher toughness.
Read MoreIt is fine dispersed carbide in a ferrite needle-like matrix. Lower bainite has lower tensile strength (about 5-10%), but usually same hardness as martensite structures, but with a higher toughness.
2 :: What are the properties and application of manganese steel?
Steel is an alloy of iron and carbon, consisting of iron phase and iron carbides. Crude steel produced from iron contains an undesirable amount of oxygen and some sulphur. Manganese plays a key role because of two important properties: its ability to combine with sulphur and its powerful deoxidation capacity. When there is insufficient manganese, the sulphur combines with iron to form a low melting point sulphide, which melts at hot rolling temperatures, causing a surface cracking phenomenon known as “hot shortness”. Desulphurization processes reduce the need for manganese in this respect. Some 30 of the manganese used today is still used for its properties as a sulphide former and deoxidant.
The other 70 of the manganese is used purely as an alloying element. These alloying uses depend on the desired properties of the steel being made. Steel, as has been noted, contains iron and carbon. At room temperature, iron crystallizes into a body-centered cubic structure named alpha iron (ferrite). At a high temperature (above 910 degrees C), the structure is transformed into a face-centered cubic form, which is called a gamma iron (austenite). When the steel is cooled down slowly, the carbon, soluble in austenite, precipitates as iron carbide called cementite, the austenite transforms to ferrite and they precipitate together in a characteristic lamellar structure known as pearlite.
Read MoreThe other 70 of the manganese is used purely as an alloying element. These alloying uses depend on the desired properties of the steel being made. Steel, as has been noted, contains iron and carbon. At room temperature, iron crystallizes into a body-centered cubic structure named alpha iron (ferrite). At a high temperature (above 910 degrees C), the structure is transformed into a face-centered cubic form, which is called a gamma iron (austenite). When the steel is cooled down slowly, the carbon, soluble in austenite, precipitates as iron carbide called cementite, the austenite transforms to ferrite and they precipitate together in a characteristic lamellar structure known as pearlite.
3 :: What is the metallurgical explanation of effects of chromium, nickel, molybdenum, and carbon in stainless steels?
Alloying elements in stainless steels can be divided into 2 main categories namely austenite and ferrite stabilizers. Austenite stabilizers must be present in austenitic as well as martensitic STSs (austenite at annealing temperature is the precursor phase for these two categories although for the latter group, it transforms to martensite before cooling down to room temperature). In order to stabilize austenite at annealing temperature, the ratio of austenite to ferrite stabilizers must be high. The strongest austenite stabilizers are N, C, Ni, Mn, and Cu whereas elements like Cr, Si, Nb, Ti, and Mo are the most important ferrite stabilizers. Ni-equivalent to Cr-equivalent ratio is an effective way to quantify the austenite formation tendency of STSs. There are different expressions for Creq and Nieq, one of which looks like this: Nieq=Ni+0.3Mn+22C+14.2N+Cu, and Creq=Cr+1.37Mo+1.5Si+2Nb+3Ti).
Read More4 :: What is the difference between diagrams of IT and CT in heat treatment of steels?
Isothermal Transformation (IT) and Continuous Transformation (CT) diagrams are diagrams used to investigate kinetic aspect of phase transformations and are of extensive use in steels heat treatment. In these diagrams generally called Time-Temperature-Transformation (TTT), the abscissa is time in logarithmic scale and ordinate is temperature. The C shaped curves indicate the onset and the end of diffusion (civilian) transformations e.g. pearlite or bainite formation or precipitation of carbides.
IT diagram shows what happens when steel is held at a constant temperature for a prolonged period. The development of the microstructure with time can be followed by holding small specimens in a lead or salt bath and quenching them one at a time after increasing holding times and measuring the amount of phases formed in the microstructure with the aid of a microscope. An alternative method involves using a single specimen and a dilatometer, which records the elongation of the specimen as a function of time. The basis for the dilatometer method is that the micro constituents undergo different volumetric changes and thus, the onset of transformations could be detected.
Read MoreIT diagram shows what happens when steel is held at a constant temperature for a prolonged period. The development of the microstructure with time can be followed by holding small specimens in a lead or salt bath and quenching them one at a time after increasing holding times and measuring the amount of phases formed in the microstructure with the aid of a microscope. An alternative method involves using a single specimen and a dilatometer, which records the elongation of the specimen as a function of time. The basis for the dilatometer method is that the micro constituents undergo different volumetric changes and thus, the onset of transformations could be detected.
5 :: How can you separate gold from mercury?
1. Gold (Au) and mercury (Hg) are two separate metals. Therefore, from pure mercury you cannot extract Gold.
2. Amalgamation is better suited to ores in which the gold occurs in the free and cores state. Fine particles of Gold are better treated by Cyanidation.
3. Gold dissolves in aqua regia. Aqua Regia is a mixture of hydrochloric acid and nitric acid. It can dissolve gold, which single acids alone cannot do. Here we see that each of the acids separately has no effect on the gold but a mixture of the two dramatically reacts with the gold. To three samples of gold are added (1) concentrated hydrochloric acid (2) concentrated hydrochloric and concentrated nitric acids and (3) concentrated nitric acid. The gold reacts only with the concentrated acid mixture which is referred to as aqua regia (royal water)".
Read More2. Amalgamation is better suited to ores in which the gold occurs in the free and cores state. Fine particles of Gold are better treated by Cyanidation.
3. Gold dissolves in aqua regia. Aqua Regia is a mixture of hydrochloric acid and nitric acid. It can dissolve gold, which single acids alone cannot do. Here we see that each of the acids separately has no effect on the gold but a mixture of the two dramatically reacts with the gold. To three samples of gold are added (1) concentrated hydrochloric acid (2) concentrated hydrochloric and concentrated nitric acids and (3) concentrated nitric acid. The gold reacts only with the concentrated acid mixture which is referred to as aqua regia (royal water)".
6 :: What does allotropic mean what does iron and steel have to do with it?
Iron is a metal with polymorphism structure. Each structure stable in the range of temperature, for example delta-iron with bcc structure in the range of 1538-1394C changes to gamma -Iron with fcc in the range of 912-1394C and gamma iron to Alfa-Iron etc. For hardening of the metal, this quality of iron is exploited.
Read More7 :: Why we are doing post heating in alloy steel welding?
The preheating is application of heat to a base metal immediately before welding. Preheating helps reduce hardness in the metal.
In addition, the application of heat to the weld immediately after welding is post-heating .The Post heating helps reduce stress in the weld metal.
Read MoreIn addition, the application of heat to the weld immediately after welding is post-heating .The Post heating helps reduce stress in the weld metal.
8 :: When we do cardonitriding or casehardening operation for a plain carbon steel the case depth, hardness & microstructure are not alike why and what are the basic thing, which makes such a difference.
Usually that will depend on the time and temperature, as well as chemical composition of the furnace atmosphere you are using.
If these variables are not kept well controlled, they may cause very different results. Please note that time and temperature are correlated, the more temperature, the less time and lesser diffusion control.
Read MoreIf these variables are not kept well controlled, they may cause very different results. Please note that time and temperature are correlated, the more temperature, the less time and lesser diffusion control.
9 :: What is or what characterize the thermodynamic state of metal (structure of metal)?
In the solid state, metals have a crystalline structure made of metal atoms, which are drawn together by low force vanderwaals interactions. The electrons form a cloud around the atom structure and migrate from one point to the other constantly.
The structured state of the atoms allows for low entropy in this state. Depending on the metal, several different structures may form, and one metal may have more than one structure at different temperatures, since its entropy depends on atom vibration as well, which is connected to the internal energy, reflected as temperature.
Crystalline structures have, usually, a straight correlation of stress in the elastic region. When traction stress is applied, the atoms are forced away from each other, up to a point where it, theoretically, should loose coherence by breaking all interactions at once and forming new surfaces. This energy level is so high that other mechanisms of energy dissipation happen first, usually connected to defects and dislocations in the crystalline structure. These mechanisms allow for the inducing of surface cracking, or plastic deformation.
Read MoreThe structured state of the atoms allows for low entropy in this state. Depending on the metal, several different structures may form, and one metal may have more than one structure at different temperatures, since its entropy depends on atom vibration as well, which is connected to the internal energy, reflected as temperature.
Crystalline structures have, usually, a straight correlation of stress in the elastic region. When traction stress is applied, the atoms are forced away from each other, up to a point where it, theoretically, should loose coherence by breaking all interactions at once and forming new surfaces. This energy level is so high that other mechanisms of energy dissipation happen first, usually connected to defects and dislocations in the crystalline structure. These mechanisms allow for the inducing of surface cracking, or plastic deformation.
10 :: What are the compositions of brass, how can this metal be heat-treated, what is the melting point of this metal?
Brass is an alloy of copper and zinc, with varying degrees of mixing. It is a substitution alloy, which means the copper and zinc elements substitute each other in microstructure matrix positions. This behavior translates into a metal which has a lower melting point in between that of its elements (Cu=1084, 83ºC, Zn=419, 58ºC) in pure state. Usually, the possibility of heat treatment will depend on what are you trying to achieve. For the substitution range of compositions, for example, you cannot obtain hardening from heat-treating.
Read More11 :: How we describe strain aging based on dislocation theory?
The carbon/nitrogen atoms are important in yielding process because they interact with the dislocations and immobilize them. This locking of the dislocations is brought about because the strain energy due to the distortion of a solute atom can be relieved if it fits into a structural region where the local lattice parameter approximates to that of the natural lattice parameter of the solute. Such a condition will be brought about by the segregation of solute atoms to the dislocations, with large substitution atoms taking up lattice positions in the expanded region, and small ones in the compressed region; small interstitial atoms will tend to segregate to interstitial sites below the half-plane. Thus, where both dislocations and solute atoms are present in the lattice, interactions of the stress field can occur, resulting in a lowering of the strain energy of the system. This provides a driving force tending to attract solute atoms to dislocations and if the necessary time for diffusion is allowed, a solute atom 'atmosphere' will form around each dislocation.
Read More12 :: How does and why the recrystallization temperature of the metals affects on alloying?
The formation of new equi-axed grains in the heating process, instead of the oriented fibrous structure of the deformed metal is called re crystallizations. The temperature required for the beginning of the re crystallizations is characteristic of each metal but depends on number of factors and firstly up on the degree of deformation. The higher the degree of deformation, the lower the re crystallizations temperature will be.
In the process of the re crystallization of such metals as iron, copper, and aluminum, the new crystals sometimes grow in an oriented arrangement and the so called re crystallization texture is obtained.
The effect of foreign atoms in solid solution on the rate of re crystallization is almost apparent at very concentrations. The change in the re crystallization temperature caused by the presence of foreign atoms depends markedly up on the nature of the solute atoms.
Read MoreIn the process of the re crystallization of such metals as iron, copper, and aluminum, the new crystals sometimes grow in an oriented arrangement and the so called re crystallization texture is obtained.
The effect of foreign atoms in solid solution on the rate of re crystallization is almost apparent at very concentrations. The change in the re crystallization temperature caused by the presence of foreign atoms depends markedly up on the nature of the solute atoms.
13 :: What is proeutectoid ferrite and cementite?
If you are not familiar with the Fe-C binary phase diagram, please try to download it before reading the answer below, because without such prior knowledge, it might be difficult to figure out my answer. Using keywords "Fe-C", "phase", and "diagram" in search engines like Google, you can easily find this diagram.
As you probably know, in the iron-carbon binary phase diagram, which in addition to some other purposes is used to predict phase transformations in steels and cast irons, there, is a eutectoid reaction wherein austenite phase decomposes to a mixture of ferrite and cementite upon cooling. If there is no alloying element other than carbon, and if cooling rate is slow enough (so that there is sufficient time for diffusion transformations to take place), this reaction occurs at the temperature of ~723C and at a composition of ~0.8wt%C; a Fe-C alloy with exactly 0.8wt%C is called a eutectoid steel.
Read MoreAs you probably know, in the iron-carbon binary phase diagram, which in addition to some other purposes is used to predict phase transformations in steels and cast irons, there, is a eutectoid reaction wherein austenite phase decomposes to a mixture of ferrite and cementite upon cooling. If there is no alloying element other than carbon, and if cooling rate is slow enough (so that there is sufficient time for diffusion transformations to take place), this reaction occurs at the temperature of ~723C and at a composition of ~0.8wt%C; a Fe-C alloy with exactly 0.8wt%C is called a eutectoid steel.
14 :: What is the metallurgy use? What is the casting and forging?
Actually, you asked a question, which requires a very long-winded answer. In summary, actually, you asked a question, which requires a very long-winded answer. In summary, metallurgy i.e., science of metals, is used to get metals with higher quality and higher in-service performance.
Casting is a forming method based on melting metals and pouring them into molds with desired shapes, so that after solidification desired properties are achieved.
Forging is a solid state forming method, which means it involves no melting. Forging stock is heated up to the appropriate temperature (it is usually so hot that appears red or white) and then application of pressure leads to plastic deformation of stock. Therefore, stock takes on the negative shape of die. Heating facilitates forming, i.e. makes possible forming at a smaller load.
Forging products usually are of higher quality and have a higher manufacturing cost compared to castings. Some parts cannot be used in the cast form because of the defects inherent to casting (most grades of steels) while some other metals are so brittle that they cannot be forged (e.g. cast irons). Indeed, there are some metals, which can be produced by either of the methods. The standard applicable to the part determines which form must be used.
Read MoreCasting is a forming method based on melting metals and pouring them into molds with desired shapes, so that after solidification desired properties are achieved.
Forging is a solid state forming method, which means it involves no melting. Forging stock is heated up to the appropriate temperature (it is usually so hot that appears red or white) and then application of pressure leads to plastic deformation of stock. Therefore, stock takes on the negative shape of die. Heating facilitates forming, i.e. makes possible forming at a smaller load.
Forging products usually are of higher quality and have a higher manufacturing cost compared to castings. Some parts cannot be used in the cast form because of the defects inherent to casting (most grades of steels) while some other metals are so brittle that they cannot be forged (e.g. cast irons). Indeed, there are some metals, which can be produced by either of the methods. The standard applicable to the part determines which form must be used.
15 :: Which is the only liquid in which gold is dissolved?
Since gold is very a noble metal, it does not dissolve in conventional solvents used to leach. Gold cannot be easily converted to Au2+ cations, so in practice, it becomes dissolved in the form of complex cations Au((CN)2)-, using the alkaline cyanide solutions like sodium cyanide, indeed in the presence of oxygen as oxidant(usually air agitation is used).
Read More16 :: How much gold concentration should be in the organic phase (DBC) before reduction by oxalic acid solution? Is it effective on purity of gold in reduction step? What is the ratio of DBC to oxalic acid solution in this step?
It really does not matter the concentration of gold in the DBC, it will respond well to very small concentrations or it will generally load up at about 25 grams of gold in a liter of DBC. This does not present a problem, as the DBC is completely re-useable, although I generally figure on a 3% to 4% loss per cycle in handling, etc. Therefore, if your original acid had 50 grams of gold in it, you would do two extractions into DBC using a liter of the extracting solvent. You should continue to extract from the pregnant gold solution until you are sure no gold is left in it. If the pH of the acid solution is not too high a simple stannous chloride test will tell you if there is still gold in it, and that is sensitive to the ppb level.
Read More17 :: How is solution annealing carried out? What type of furnace is required? Does one need to be heat in a Salt Bath?
Solution annealing is carried out by heating up the alloy to a temperature in which typically only one phase is stable. This temperature depends on the alloy to be solution heat-treated; for precipitation hardenable Al-Cu base alloys, solution-annealing temperature is ~550C in which only alpha phase persists and for some precipitation hardenable steel grades like precipitation hardening martensitic stainless steel 17-4PH, this is something like 1050C where only gamma (austenite) phase exists.
Solution annealing is the second stage of a two-stage process; the second stage is precipitation hardening which is performed by heating the alloy to a temperature far below the solution annealing temperature, in which very small precipitates begin to form. This leads to enhancement of mechanical properties of the alloys and desired properties mainly high strength are reached only at the end of the precipitation hardening stage, whereas after solution annealing, material is rather soft. The precipitation hardening temperature for Al-Cu base alloys is something around 180C, while that of 17-4PH stainless steel is around 500C. Such materials are mainly used in aerospace applications where materials having high strength/weight ratios are required.
Read MoreSolution annealing is the second stage of a two-stage process; the second stage is precipitation hardening which is performed by heating the alloy to a temperature far below the solution annealing temperature, in which very small precipitates begin to form. This leads to enhancement of mechanical properties of the alloys and desired properties mainly high strength are reached only at the end of the precipitation hardening stage, whereas after solution annealing, material is rather soft. The precipitation hardening temperature for Al-Cu base alloys is something around 180C, while that of 17-4PH stainless steel is around 500C. Such materials are mainly used in aerospace applications where materials having high strength/weight ratios are required.
18 :: Will aluminum alloy like 380 or 356 settle? Meaning while in "Liquid form" above melting point will the heavier elements like copper, Fe, Silicon, zinc etc. settle to the bottom of the liquid/molten aluminum after a period.
Yes settling, due to gravity, of heavier elements takes place in the molten state in the absence of any convection. As you know, severity of settling depends on the density difference among alloying elements. For instance, in the case of A356 alloy, the main elements Al and Si have rather similar densities and settling of Al is too sluggish. Nevertheless settling of heavy elements like Cu may lead to their accumulation in the bottom of container after a rather short time, provided there is NO convection. In practice, settling in the molten state is not too likely and will not be problematic.
In contrast, during soaking in the semi-solid state, settling would be considerable since presence of a network of primary dendrites interferes with convection in the liquid phase. My own experiments have evidenced considerable settling of Zn in the case of ZA27 alloy (Zn-28.5wt%Al-2.5wt%Cu) after a soaking time of 55 minutes in the semi-solid state (452C). Normally for this alloy primary dendrites are Al-base (refer to Al-Zn binary phase diagram) but due to Zn settling, primary phase in the bottom of container had changed to a Zn-base phase which will only form when zinc content is more than 98wt% or so. Primary dendrites at the upper part of container were Al-base
Read MoreIn contrast, during soaking in the semi-solid state, settling would be considerable since presence of a network of primary dendrites interferes with convection in the liquid phase. My own experiments have evidenced considerable settling of Zn in the case of ZA27 alloy (Zn-28.5wt%Al-2.5wt%Cu) after a soaking time of 55 minutes in the semi-solid state (452C). Normally for this alloy primary dendrites are Al-base (refer to Al-Zn binary phase diagram) but due to Zn settling, primary phase in the bottom of container had changed to a Zn-base phase which will only form when zinc content is more than 98wt% or so. Primary dendrites at the upper part of container were Al-base
19 :: How can you find out what kind of stainless steel was used in making a stainless object?
Usually, one can simply guess the general type of stainless steel i.e. tell if it is ferritic (or martensitic) or austenitic though there are some other types of stainless steels like precipitation hardening and duplex types which have some specific applications. To find the category to which you are stainless belongs, you only need a magnet. If the magnet attracts your steel, then it is a ferritic (martensitic) type otherwise austenitic. Austenitic steels have high nickel or manganese contents, which are both austenite stabilizer elements. However, you need to perform further examinations to tell the exact grade of your steel. These examinations might be micro structural, compositional etc. Usually purchasers of stainless use a quantometer to find chemical composition of stainless steels; then they compare the compositions with the standards and find their type. Please note that only limited grades of stainless steels like 410, 420, 201, 304, and 316 are frequently used and usually one only needs to tell these from each other.
Read More20 :: What is the grain size of lead as an element and as an alloy such as lead tin alloy?
Grain size in alloys and pure elements is a function of their solidification rate. The higher the solidification rate, the smaller the grains are. Determination of grain size in pure elements is rather difficult since it is difficult to locate the grain boundaries; there is no segregation and composition distinction in the case of micro structural features in pure elements. However, in the case of alloys such as Pb-Sn alloys, composition difference between the primary dendrites and the eutectic matrix allows for grain size measurement. As most of Pb-Sn alloys exhibit a dendritic structure surrounded in a eutectic matrix, the dendrite arm spacing is used instead of grain size. For some alloy systems, there are relationships to correlate grain size to solidification rate. In the case of pure Pb and Pb-Sn alloy as well as most other alloys, primary dendrite arm spacing (at normal solidification rates like those applicable through sand and even die casting) is of order some microns and can be decreased to some nanometers by Rapid Solidification processes like melt spinning. The solidification rate in the case of such processes can reach 1,000,000,000 [0C/s]. These processes have the capability of producing "Amorphous" structures in the case of some special alloys where grain size becomes meaningless. For more information on lead alloys, you are advised to refer to the 2nd volume of ASM handbooks, which is on non-ferrous alloys and contains a section devoted to lead alloys.
Read More21 :: We make aluminum moulds by press casting, can u suggest any thing so that the moulds should shine after casting?
Shininess of castings depends on the surface quality of cast parts. Casting surface finish is always a function of mold surface and characteristics. The selection of mold materials and the accuracy of mold finish maintained in premium casting operations ensure that specified requirements are met. Sometimes there is the possibility of increasing surface finish of castings by increasing their surface tension. This is done for aluminum alloys by allowing formation of oxide inclusions, the most important of which is Al2O3, in the molten metal. The increase in surface tension prevents molten metal from penetrating into the mold depressions since as you know surface finish improves when the melt solidifies in contact with air. However, such a resolution is accompanied by decrease in mechanical properties of castings, as oxides will act as stress concentration sites.
By the way, I have not heard about usage of grain refiners as shine promoters for aluminum castings, though their application in such cases may rely on the same mechanism.
Read MoreBy the way, I have not heard about usage of grain refiners as shine promoters for aluminum castings, though their application in such cases may rely on the same mechanism.
22 :: What is the difference between plaster used in gold investment casting and ceramic used in the process of investment casting of automobile engine parts and turbine blades etc. when both are used in the lost-wax method?
In general, the plaster used in gold investment casting is standard "plaster of Paris" or other such material it has a fine but inconsistent grain size and, for the most part, water based. The other parts you mentioned are generally a higher precision, the casting material is of a fine but consistent grain, high temperature, hard, and not always water based. This is especially important for turbine blades as the material from which they are cast is more difficult to fine finish than other metals and the precision is extremely important due to the speed of rotation. It would be safe to say that the latter could be used in place of the former but not the former in place of the latter. Hope this is helpful.
Read More23 :: Does the extrusion process for A355 AND A356 alloy effect on the amount of impact energy?
Yes, it does. I am not an expert in these things, but I do know that the parameters of the extrusion process directly affect the crystalline matrix of the alloy, which in turn governs the physical characteristics of the alloy. As the differences can be quite significant, I would recommend checking with qualified references for pertinent details. I know that quenching and max temperatures are big issues. Good luck, sorry I could not be of greater assistance.
Read More24 :: Does case harden steel properties detoriates over time? Especially for guns, parts like bolt carrier, the brand new parts has been kept for 10 year and properly oiled. I am worried about its surface hardness to take the blow during firing.
Hardened steel does not generally deteriorate over moderate periods, especially not as short as ten years, providing it have been protected from corrosion. Strong magnetic fields and electric fields generated through or around the steel can have an effect, but this is highly unlikely. If your bolt carrier has been kept protected and oiled it should be fine. I have a shotgun that was made in 1740 which has lost none of its hardness as well as steel swords dating back to the 1600's that are still hard and sharp. You should not have a problem.
Read More25 :: How is metal heavy?
Not all metals are heavy. Hydrogen is a metal, and is the lightest element known. Lithium, also a metal is the third lightest element there are many heavy elements that are not metals. If you "Google" the definition of "metal" you will note the properties that qualify a substance as a metal. Mass (weight) is not the important factor. Common metals are heavy because they have a dense electron structure.
Read More