Construction Welder Interview Questions And Answers
Prepare comprehensively for your Construction Welder interview with our extensive list of 100 questions. Each question is designed to test and expand your Construction Welder expertise. Suitable for all experience levels, these questions will help you prepare thoroughly. Don't miss out on our free PDF download, containing all 100 questions to help you succeed in your Construction Welder interview. It's an invaluable tool for reinforcing your knowledge and building confidence.
100 Construction Welder Questions and Answers:
Construction Welder Job Interview Questions Table of Contents:
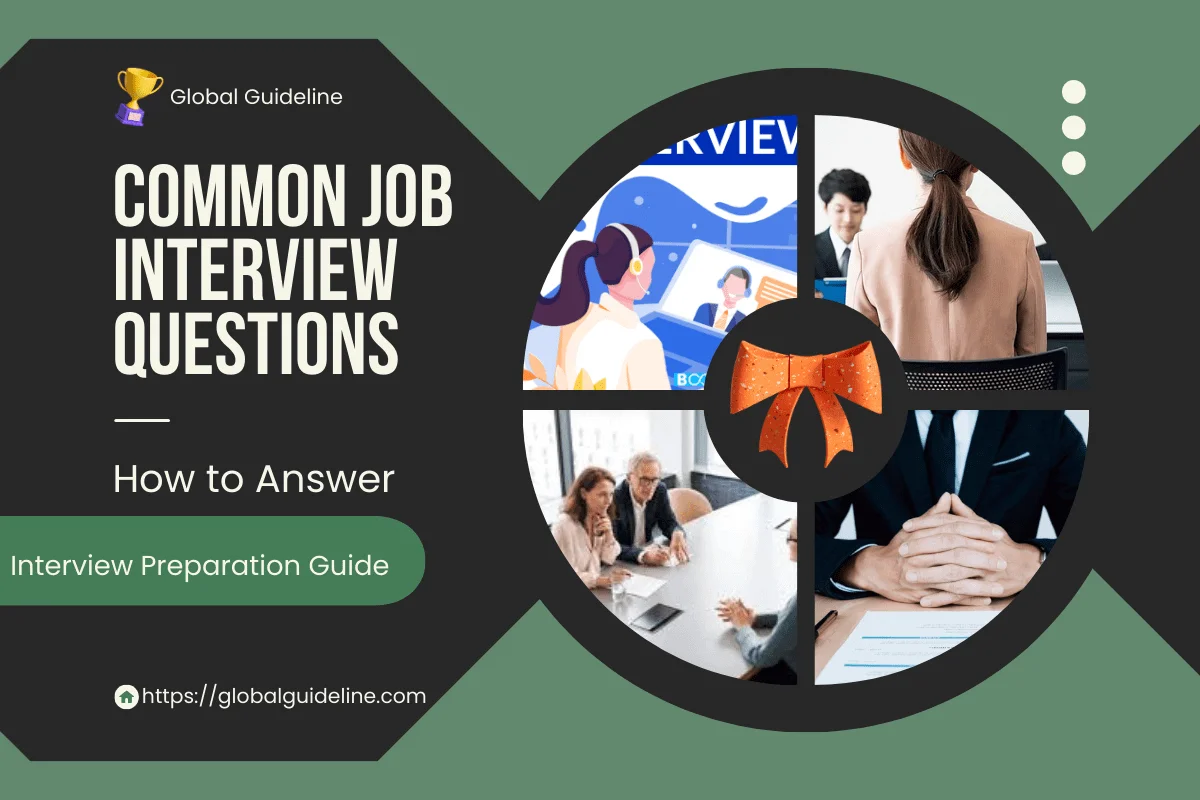
1 :: Tell me what are the duties of structural Iron and Steelworker?
☛ Build steel and or iron girders, columns and other construction based structures
☛ Make, weld and bolt down steel bars to reinforce concrete
☛ Connect steel columns, beams, and girders
☛ Reinforce concrete with welded wire fabrics
☛ Position steel or iron structures with connecting bars and spud wrenches
☛ Check the alignment using plumb bobs, levels, and laser equipment
☛ Fasten bars together with wire
☛ Drill holes into steel for bolts
☛ According to assembly instructions number the steel structures
☛ Hoist steel into the framework
☛ Inspecting material and equipment’s
Read More☛ Make, weld and bolt down steel bars to reinforce concrete
☛ Connect steel columns, beams, and girders
☛ Reinforce concrete with welded wire fabrics
☛ Position steel or iron structures with connecting bars and spud wrenches
☛ Check the alignment using plumb bobs, levels, and laser equipment
☛ Fasten bars together with wire
☛ Drill holes into steel for bolts
☛ According to assembly instructions number the steel structures
☛ Hoist steel into the framework
☛ Inspecting material and equipment’s
2 :: Tell me what is blue print reading?
Blueprint reading is like a structural map that covers the steel structure. It is a detail drawing of steel structure, and it carries a label or piece mark to differentiate one steel bar or structure from others. Each piece or segment of steel structure has a single blueprint with detailed information before it become the part of the whole. It carries information even small as hole sizes, dimension, etc.
Read More3 :: Explain me on what three factors does rigging process depends on?
Rigging process depends on three factors
☛ Capacity of the hoisting device
☛ Working loads of ropes and hardware
☛ Weight of the load to be lifted
Read More☛ Capacity of the hoisting device
☛ Working loads of ropes and hardware
☛ Weight of the load to be lifted
4 :: Tell me what is the specification/classification for carbon steel Electrode?
AWS 5.1/E-XXXX
Read More7 :: Tell me if welder made test by 2’’ dia, what is his range qualified?
He has qualified 1’’-dia and above.
Read More8 :: Tell me how much percentage is allowed more than test pressure in Pressure relief device?
Test pressure plus10% (10% should be lesser than 50Psi).
Read More9 :: What is PQR?
PQR stands for procedure qualification record. The PQR documents what occurred during welding the test coupon and the results of testing of the coupon.
Read More11 :: Tell me what is the drying temperature for Stainless Steel electrodes?
120 to 250 degree temperature.
Read More12 :: Tell me where we can use E-6010 type electrode?
we can use at root pass for deep penetration
Read More13 :: Explain what is the standard for liquid Petroleum Transportation piping systems?
ASME B31.4
Read More14 :: Tell me what care has to be taken while operating power tools?
While, operating power tools following thing has to be taken care
☛ Maintain and inspect power tools on a regular basis
☛ Discard defective tools
☛ To avoid accident tool must be provided with “dead man” trigger or power off switch
☛ Use only those tools that are certified
☛ Avoid using any rotatory screw with a protruding set screw that can catch current
☛ Do not keep any tool hanging or swaying out of your pocket exposed to electric wire or tool
☛ Do not rely on wire, rods or other makeshift material, right tool should be used to do the job
Read More☛ Maintain and inspect power tools on a regular basis
☛ Discard defective tools
☛ To avoid accident tool must be provided with “dead man” trigger or power off switch
☛ Use only those tools that are certified
☛ Avoid using any rotatory screw with a protruding set screw that can catch current
☛ Do not keep any tool hanging or swaying out of your pocket exposed to electric wire or tool
☛ Do not rely on wire, rods or other makeshift material, right tool should be used to do the job
17 :: Tell me which type of electrode we are using in GTAW process?
Non-Consumable Tungston Electrode
Read More18 :: Tell me what is the standard for welding rods Electrodes and filler metals?
ASME Sec-IIC
Read More21 :: If welder made test by 14 mm thickness, what is his thickness range qualified?
He has qualified unlimited thickness.
Read More24 :: Tell me what is meaning for SAES, SAEP and SAMSS?
Saudi Aramco Engineering Standards
Saudi Aramco Engineering Procedures
Saudi Aramco Materials System Specification
Read MoreSaudi Aramco Engineering Procedures
Saudi Aramco Materials System Specification
25 :: Tell me how much area is required for Pre-heat?
75 mm minimum from both end of the Joint.
Read More