Material Manager Interview Questions And Answers
Prepare comprehensively for your Materials Manager interview with our extensive list of 84 questions. Our questions cover a wide range of topics in Materials Manager to ensure you're well-prepared. Whether you're new to the field or have years of experience, these questions are designed to help you succeed. Don't miss out on our free PDF download, containing all 84 questions to help you succeed in your Materials Manager interview. It's an invaluable tool for reinforcing your knowledge and building confidence.
84 Materials Manager Questions and Answers:
Materials Manager Job Interview Questions Table of Contents:
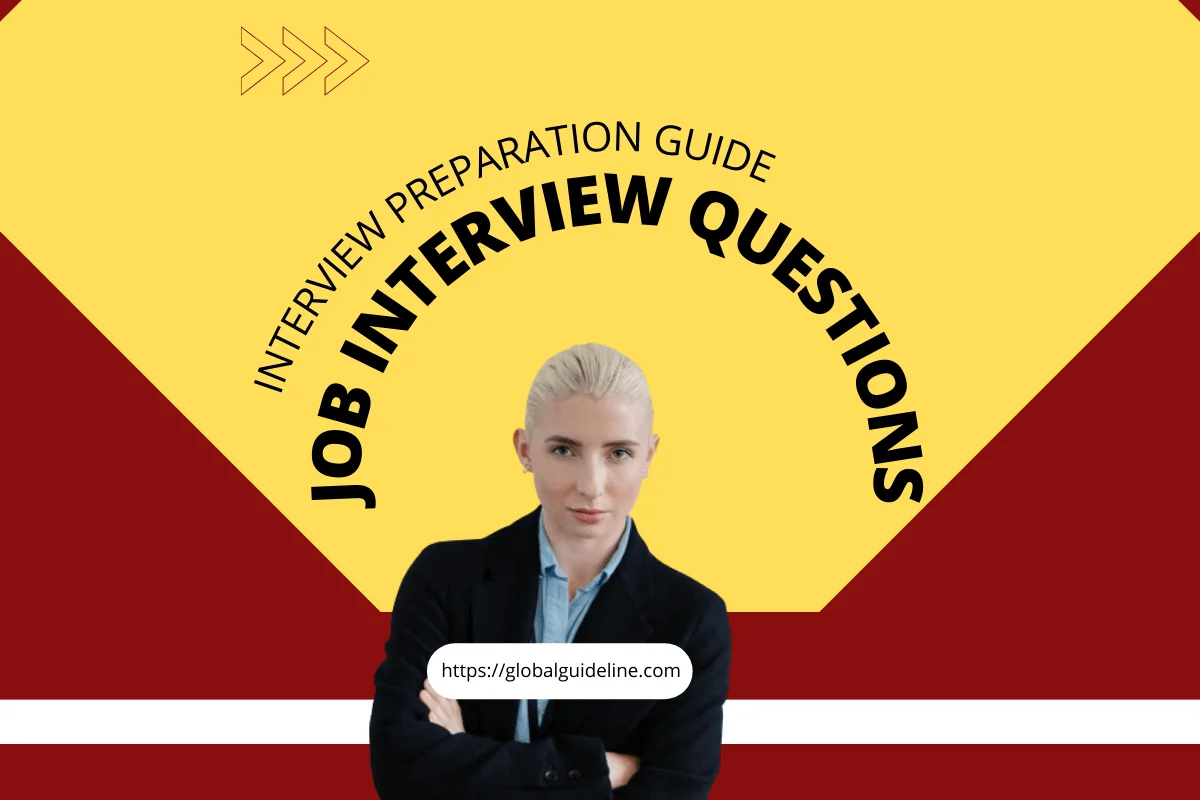
1 :: What is inventory control?
Inventory control is the process of reducing inventory costs while remaining responsive to customer demands. By this definition a store would want to lower its acquisition, carrying ordering and stock-out costs to their lowest possible levels. However a store would need to have enough inventories to meet any needs of its customers.
Read More2 :: What does inventory affect in a store?
Inventory levels and their values can affect the income of the store, the amount of taxes paid, and the total stocking cost.
Read More3 :: What if there is no savings or the models produce even results?
If there is no savings a error in the calculations may have occurred or the model does not fit your case. For instances were the total stocking costs are even you may use either order quantity.
Read More4 :: What is total stocking cost?
Total stocking cost is the cost to the store of holding a good in its inventory. The stocking cost consists of the carrying cost times half the quantity in inventory and the order completion cost times demand divided by the quantity. In its mathematical form the cost is represented by TSC=(Q/2)C + (D/Q)S.
Read More5 :: What are the kinds of info records available?
Standard, consignment, subcontracting and pipeline
Read More6 :: Tell me what do you know about SAP?
SAP stands for "Systems, Applications and Products in data processing". Amongst the software provider, SAP comes up as the world's third largest. 5 IBM employees founded SAP in 1972 in Walldorf, Germany.
Read More7 :: Explain what is difference between purchase requisition and purchase order?
Purchase requisition is an internal document and it is a request that is made to purchasing organization to procure certain list of material while purchase order is formal document that is given to vendor containing list of items to be procured from vendor.
Read More8 :: Tell us what do you understand by posting period?
Various documents like purchase order, request for quotation, goods receipt are essential documents in a business. These documents need security i.e. if any of documents is posted incorrectly then business can be affected at various concern levels. So, to secure these documents we have a concept of posting period. Posting period means it will allow you to post and make changes in the documents only in a specific time period.
Read More9 :: How can the value of inventory be determined?
The value can be found using four methods in inventory control. The first is the specific cost in which each item's cost is added together for the inventory's value. A second method is to use the weighted average of the costs for a period to determine value. A third method is first in, first out. In this method value is measured using the latest costs of goods while working towards the beginning of the period until all goods in inventory are valued. The final method is last in, first out. In this method the costs of gods at the beginning of the period are used to determine the inventory's value much like FIFO.
Read More10 :: Do I need to recompute stocking costs for the EOQ level?
Yes, in order to compare stock costs when using the EOQ model you must compute the costs for both the original level and the EOQ level of order quantities.
Read More11 :: What is a release strategy? What are release groups and codes?
The procurement process in SAP needs to be controlled by introducing authorizations at important stages. This is taken care by the release strategy, which has different codes for assigned users. For example, if the value of a PO is more than a certain pre-defined limit, then it has to be approved by the SCM manager with a certain release code. Every company will have different approval mechanisms and the release strategy can be defined by the users.
Release groups are a set of release codes that are used for authorizing a purchasing document or approving a release strategy. Release code is a 2-character ID that allows a person to approve or clear a PR or a PO and they are controlled by a step-by-step authorization system. For example, Code 10 is assigned to the person who creates the PO, Code 20 is the release code assigned to the Purchase manager for approval. Subsequently, the Department Head will use Code 30 to approve the release strategy, followed by the Operations Director, who will use Code 40 for final approval.
Read MoreRelease groups are a set of release codes that are used for authorizing a purchasing document or approving a release strategy. Release code is a 2-character ID that allows a person to approve or clear a PR or a PO and they are controlled by a step-by-step authorization system. For example, Code 10 is assigned to the person who creates the PO, Code 20 is the release code assigned to the Purchase manager for approval. Subsequently, the Department Head will use Code 30 to approve the release strategy, followed by the Operations Director, who will use Code 40 for final approval.
12 :: Explain what are Features of SAP ERP?
SAP is an enterprise resource planning software which is produced by the German corporation. SAP is a enterprise information software that was basically designed to manage resources, information and activities that are required to complete business processes like procurement and managing orders, billing of orders and management of human resources.
Read More13 :: Explain what is quota arrangement?
A particular material can be procured from different vendors depending upon the requirement. So, total requirement of a material is distributed to different vendor's i.e. quota is assigned to each source of supply. This is known as quota arrangement.
Read More14 :: What are the important considerations in inventory control?
For inventory control to work at its best a store must consider the costs of acquisition, carrying, ordering, and stock-out. the store must also look at its reordering system, its budgeting for inventory, insurance and forecasted demand.
Read More15 :: What is a order point?
A order point is a point in time at which a order is placed to replenish goods in inventory.
Read More16 :: What is MRP? And how is Lot Size used?
MRP is short for Materials Requirements Planning and it is a production planning technique that's used to manage the manufacturing process. It is basically used to determine your Material Planning procedure by specifying the various conditions like Reorder Point, Seasonal Requirement, Replenishment, Vendor Managed, Forecast Based and Master Production Scheduling (MPS). Lot size specifies the nature of material requirement in terms of Weekly, Monthly, Quantity and Maximum Replenishment.
Read More17 :: Explain what are the organizational levels in SAP R/3?
The top level of the organizational structure is the client, followed by company code, which represents a unit with its own accounting unit. The next level down is plant where procurement activities take place. A plant will produce goods and makes goods available for the company. The purchasing organization is the legally responsible for procurement transactions. This group is further subdivided into purchasing groups.
Read More18 :: Tell me what is difference between planned and unplanned services?
In planned services at the time of procurement specifications like quantity and price are known in advance. It means nature and scope of service is clear before procurement whereas in unplanned services at the time of procurement specifications like quantity and price are not known in advance. It means nature and scope of service is not clear before procurement. These services can be extended as per the requirement.
Read More19 :: Can forecasting help in controlling inventory?
Yes, through the use of forecasts inventory levels can be set to meet the demands while keeping levels as low as possible.
Read More20 :: How do you determine the numbers to use in the EOQ formula?
To determine which numbers to use you must look for the following items. The number of items per order is the quantity(Q). The number of items that can be sold is D. D may be the forecast demand for that particular good. The cost of placing the order is used for S. The final number to find is the carrying cost(C) which is the cost of the item to be held in inventory.
Read More21 :: What is interference?
Interference is a factor in forecasting demand. Interference is made up of all the factors that a forecaster has no control over. Factors that may be considered interference include natural disasters, unusual customer demands, or rare events in the business period.
Read More22 :: What do the letters in the EOQ and stocking cost formula stand for?
The letters in the formulas represent the quantity ordered(Q), the carrying cost of a unit(C), the demand for the units(D) and the cost of completing a order(S).
Read More23 :: How does the consignment cycle operate?
The various steps in consignment cycle are:
1. Create consignment info record with proper tax code 2. Create Purchase order with item category K 3. Create output condition record for KONS (output type) 4. Authorize Goods Receipt (GR) 5. Payment is settled through MRKO transaction even if invoice verification is not done
Read More1. Create consignment info record with proper tax code 2. Create Purchase order with item category K 3. Create output condition record for KONS (output type) 4. Authorize Goods Receipt (GR) 5. Payment is settled through MRKO transaction even if invoice verification is not done
24 :: What is a GR blocked stock and when is it used?
The GR blocked stock is an option used in the goods receipt process when you are not sure about the quality of the goods received. In such a case, the stock is maintained as GR blocked either from a material viewpoint or exclusively for a purchase order item.
Read More25 :: Tell us what do you mean by special stocks?
Special stocks are stocks that are managed differently as these stocks did not belong to company and these are being kept at some particular location.
Read More